A Future of Secure and Sturdy Management: Ways to Build Supply Chain Resilience
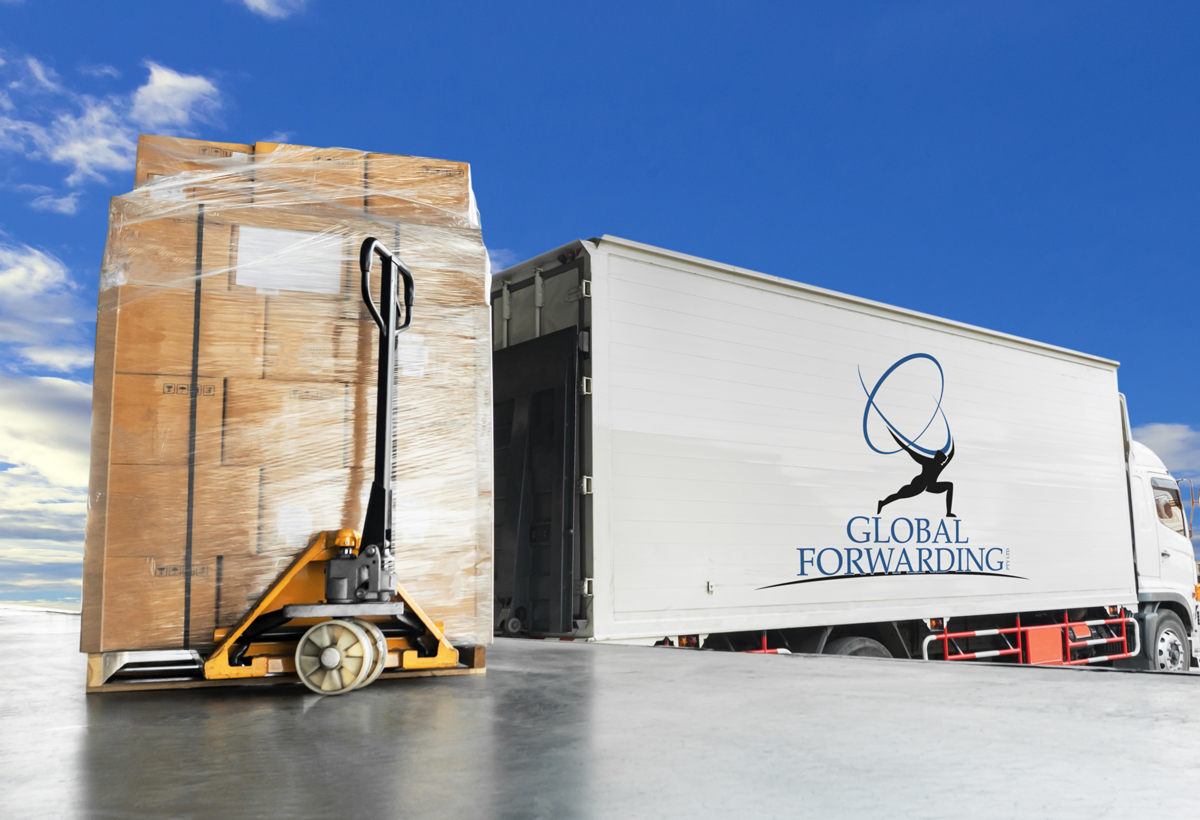
The last couple of years have been quite eventful in the supply chain industry. Disruptions seem to have come from multiple directions, from multiple sectors, pushing the industry to stay on its toes at all times.
Brexit, the exit of Britain from the European Union, has led the UK to tighten its borders. The introduction of additional custom classifications and tariffs has led to congestion at entry and exit points. This has disrupted the flow of the supply chain.
Another example of such a disruption would be the ongoing trade war between the US and China. The long-running economic conflict between the two nations, with the former hurling allegations at the latter, has created not just tension but uncertainty in the global economy.
Most recently, the COVID-19 pandemic has pushed the global supply chain industry to bring a forced stop to its activities. The pandemic sent the industry into chaos due to the unforeseen delay in activities.
These disruptions have caused the interests of the supply chain leaders to shift. They must now strike a balance between cost and operational efficiency, as well as supply chain resilience.
There have been numerous supply chain interruptions, and the one certainty is that there will be more in the future. The important takeaway is that companies who have implemented proactive resilience planning and taken proactive steps to limit structural risk in their supply chains are producing results far better than others.
Only 21% of respondents in a recent study have said that they have a highly resilient network today, which means they have good visibility and the agility to shift sourcing, manufacturing, and distribution activities around reasonably quickly. It shows that many people will prioritize building resilience when they emerge from the current crisis.
Buffers for Inventory and Capacity
Buffer capacity, whether in the form of underutilized production facilities or inventories of safety stock requirements, is the most basic way to improve resilience. The problem is that buffers are expensive. For new product launches or expansions into new growth areas, the surplus capacity of leading organizations can be used to create buffers.
Diversification of the Manufacturing Network
Many businesses have begun to diversify their manufacturing and outsourcing resources. For some, this has meant finding new suppliers outside of China or requesting that existing partners source them from other parts of Asia or nations like Mexico. Due to the increasing disruptions in the supply chain, it has become more important to invest in diversification to build resilience.
Predict, Sense & Adapt
Recognizing the impact of structural change and establishing a clear blueprint for when and how to respond to a variety of risks is critical for your supply chain management. Leaders identify four sorts of risk connected with each item or product:
- Routine interruptions
- Moderate risk occurrences
- Black swan events
- Structural faults
Businesses also need to be aware of single sources that may emerge as a result of the ripple impact of other threats. In components with two different sources, for example, a high-risk single-source situation will arise from the financial instability or depreciation of one production.
Resourcing carefully the inflection points in demand, lead time, cost, supplier financial health, and supplier consolidation across a wide range of commodities allows businesses to anticipate market movements and take proactive measures.
Utilising Various Sources
Major natural disasters in Japan and Thailand in 2011 disrupted global supply networks, exposing corporations' reliance on single sources of supply. Nearly finished cars in the automobile industry were unable to be dispatched to customers due to missing, and often inexpensive, components. Multisourcing is a straightforward technique for reducing this risk.
To develop a multisourcing strategy, supply chain leaders must have a thorough understanding of their supplier networks and be able to categorize suppliers not just by spending, but also by revenue effect in the event of a disruption. Diversification can be achieved by selecting new businesses or by collaborating with an existing single- or sole-source supplier who can manufacture in many places.
Partnerships Amoung Ecosystems
The COVID-19 incident has demonstrated the importance of a diverse sourcing strategy. Collaboration with strategic raw material suppliers and external service partners, on the other hand, is critical to ensuring future resilience. Strong connections with contract manufacturers can be critical in diversifying production and distribution to several nations for enterprises lacking the size to handle various sites on their own.
According to survey data, over half of supply chain businesses either use external manufacturers or examine how they may accommodate product changes.
What is the future of the Supply Chain?
Whatever the future holds, supply chains must seize this opportunity to transition from executors and cost centres and take advantage that unlocks operating margins. They need to embrace integrated planning with acquisition and finance.
It's time for supply chains to focus on reducing complexity, align strategies, and stay more alert for a secure and sturdy future.
Here at Global Forwarding, our team can design a taylormade supply chain strategy that suits you and your business. Contact us today for more information!